Mahyaz Engineering Company is ready to perform all pipeline operations and orbital welding of process lines and accessories, including PW, WFI, and clean steam and … as well as modifying, improving and rebuilding old lines for the pharmaceutical, food and biotechnology industries.
Having the necessary welding and assembly equipment, including orbital welding machines for automatic welding, and having an experienced technical team in this field, allows pipelines to be carried out in accordance with the standards and quality requirements, and the possibility Provide documentation and inspections.
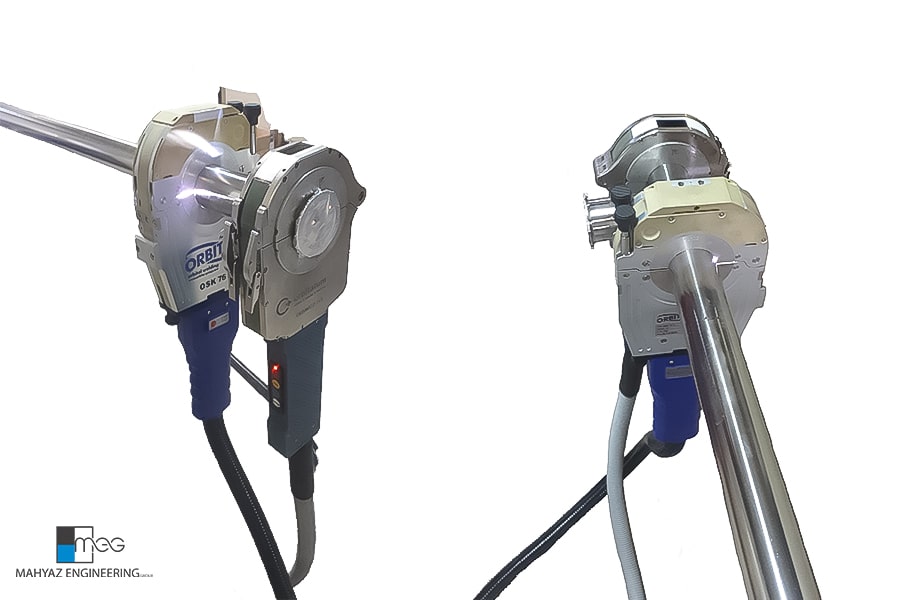
What is ORBITAL WELDING ?
The orbital welding means a continuous 360-degree arc electrical rotation around a piece of work (usually a pipe). This process was originally created due to an operator error in GTAW welding. In Orbital Welding, the computer-controlled fusion process is performed with very little operator interference. This process is specifically used for “high quality” and “high repeatability” welds.
In the 1960s, the aerospace industry needed a very precise welding process that could create hydraulic lines of planes with tungsten arc welding and inert gas. This requirement led to the development of an orbital welding method in an airline company.
For many reasons, such as different welding situations and the limited space around the connecting line, standard welding cannot be achieved manually. To fully control the boiling pond, a perfect balance between gravitational forces and surface tension should be established in any position of the arc. This is possible with planned changes in the effective factors of welding in orbital welding.
In particular, the tube welding process is performed using closed-head valves according to ASME Section 9.
An approved orbital welding sample can be 100% repeated until the welding program or the gas used is changed. Training and experience, of course, will allow operators to make acceptable bouts.
ASME considerations for the certification of a person as an orbital welding operator require a person to install the head and create a welding program with a welding machine in such a way that six successive welds can pass bending or stretching tests.
Successful Orbital Welding also depends on the quality of the tube material. Usually, only 316L stainless steel tubes (not pipes) are used in high-speed orbital welding.
Another important factor is the use of argon gas purity. Minimum purity for common industrial applications should be 99.995%. For some applications, it is necessary to use very pure argon with a purity of 99.9998% and the use of suitable equipment such as flowmeters and valves for this purity. Usually, you can not use rubber equipment for gaseous gas, because it absorbs moisture and oxygen and releases argon.
Welding samples for testing welding quality are usually required at the beginning of each shift. If any of the welding parameters, such as the welding program or the gas, is to be changed, the welding sample should be re-sampled and inspected in terms of the internal and external surfaces.
For some reasons, the orbital welding is performed on tubes and not tubes, most notably the variations in the outer diameter of the tubes.
Orbital welding today is the standard method for connecting gas and fluid systems to the semiconductor and pharmaceutical industries. Orbital welding for these industries was created commercially in the mid-1980s.
Orbital welding Advantages
-
Clean and hygienic
It is important to keep metal pipes away from contamination during the welding process because impregnated impurities can affect the whole process and cause great loss of time and money. Orbital welding is usually done in clean environments where high-purity pipes and fittings are welded and the environment is free from contamination.
-
Efficient
Since the welds obtained in this way are uniform and clean, the entire welding process is also more efficient. Computerized Orbital Welding can be even more productive because the whole process can be pre-programmed and documented, thus reducing overall operation time and costs.
-
More productive
Orbital welding is more efficient in terms of labor because machine does most the work, and this reduces the need for labor.
-
Better weld quality
Although skilled manual welders can perform a high-quality welding job for a specific purpose, you can always get better quality when used in correct orbital welding. This is very important for the health and sterilization industry.
-
Uniformed welds
Although the welds done by an experienced manual welder can be exact and regular, Orbital Welding will always have regular welds. This is because the orbital welding machine can be set up for a specific program and, as a result, it is repeated repeatedly and repeatedly without defects or forms, while for manual welds it is inherently and naturally a part of There is a difference and a lack of integrity between the boils.
-
There is no need for a certificate
Because the few number of certified welders in this field، It is difficult to find manual welder with experience and skills in this area While orbital welding does not require certification because the device can be used by a trained technician in welding field.
-
For specific problems and situations.
Orbital welding is great solution for special situations, such as those where there is no pipe rotation or space obstruction for manual welders.
-
Reduces completion time for projects
As the welding is done automatically by the machine, the speed of the welding process will be higher, while testing on one sample does not require testing for anyone.
Acceptance criteria is an important aspect of the piping system. The ASME B31.3 standard specifies the acceptance rules for welding, ie the required tests, the number of welds to be inspected, and so on. On the other side, according to ASME BPE, the boils must comply with the ASME SEC IX and ASME B31.3 standards.
Related Issues These standards should be presented in the WPS and PQR documentation, and all welders must have certificates in accordance with these standards. Also, the competence of inspectors should be approved according to the rules.
The B31.3 standard more focuses on the strength of the welds, while the BPE focuses more on the quality of the weld surfaces.
ASME B31.3 is also written for manual welding processes, whereas the ASME BPE offers automatic or orbital welding so that only if the use of orbital welding causes Dead Leg to be used, welding Manually authorized by customer approval. (In the BPE standard, in SD-3.1.2.2, the Dead Leg parameter (L / D) is defined for the purpose of pipetting biometric systems as the target value. In this definition, L is the amount of outgrowth of the main line from the outer surface of the main pipe and D The inner diameter is outflank.
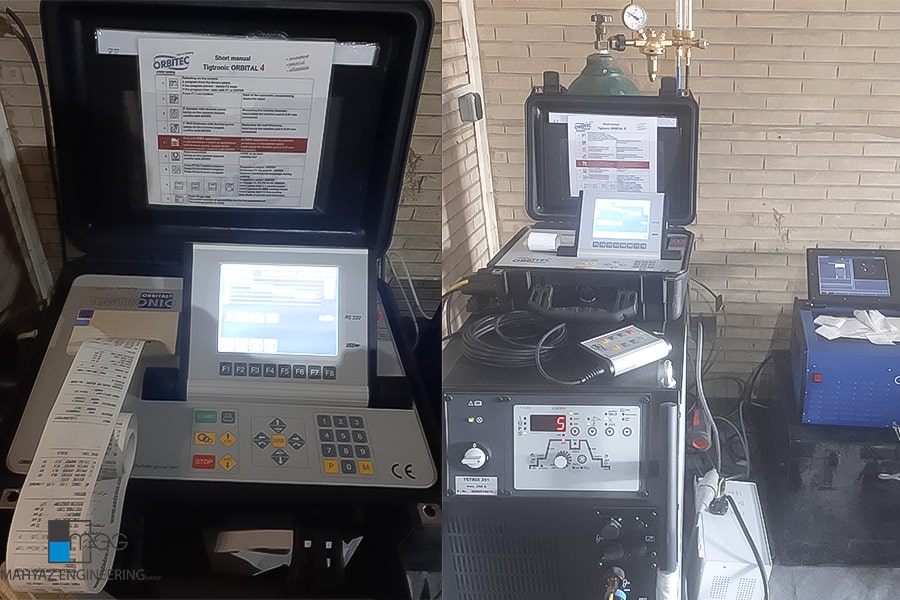
Welding inspection in piping systems
In the validation of the piping systems, the most important factor affecting the quality of water that is examined by the FDA is counting the bacteria (live) and the endotoxin. Therefore, full and seamless penetrating booms with a smooth interior surface are essential for such quality.
A plan containing details of various inspections should be made between the employer and the contractor. The ASME BPE standard states that all welds should be inspected from the outer surface of the eye, and at least 20% of the welds should be randomly inspected in the bruxism as well. The rate of defective orbital welding is very low in biotechnology applications.
Items to be considered in a piping system:
1-The piping route should be as straightforward and short as possible so that the amount of liquid CIP required to fill the circuit is minimal and may not be used with additional fittings and tubes.
2- Mixing contaminants in product flows should be eliminated with physical considerations, with different ways to do this.
3- The use of overpass lines (along with steam traps, valve controls, etc.) is not recommended.
4- The use of barrier equipment on the line due to the creation of dead space is not recommended.
5- In horizontal piping lines, non-center reducers should be used to prevent the airbags from being created in the system.
6- The system should be designed in such a way that airbags are not created in the system.
7- The radius of the line of the axis of the bends should not be less than 2.5 times the nominal diameter of the tube, in order to prevent the collapse of the inner surfaces (wrinkles or possible cracks). Of course, bends with a smaller radius can be utilized by customer agreement and using appropriate inspection methods (ocular, baroscopic, cross-sectional, etc.).
8- Gate valves are not recommended in hygienic piping routes.
9- Contact surfaces of austenitic stainless steel must be deactivated before use. There is no need to inactivate electrolyzed surfaces unless the surface is exposed to changes such as welding or mechanical payments.
10- Use of blind burns should be avoided as much as possible. Blisters are meant for welding that cannot be checked. Using the proper process of matching the components of the piping system, it can be minimized.