Purified water is an essential ingredient in the pharmaceutical industry and cell culture and other parts of the biotechnology industry. Water purity is vital and can be created with a variety of equipment and approaches that are based on other activities of the drug site.
Purified water is usually provided with multi-stage treatments of a drinking water supply (municipal). Drinking water is composed of several other sources of water, including surface water, river water, and underground aquifers, and intrinsically contaminated with it. Types of dissolved ions, organic components, particles, colloids and a range of bacteria and other living organisms are examples of water impurities. According to the region, the amount of impurities in the initial water is very different.
Mahyaz Engineering Company is one of the manufacturers of water supply systems, which is proud to offer its customers in accordance with the most up-to-date international standards.
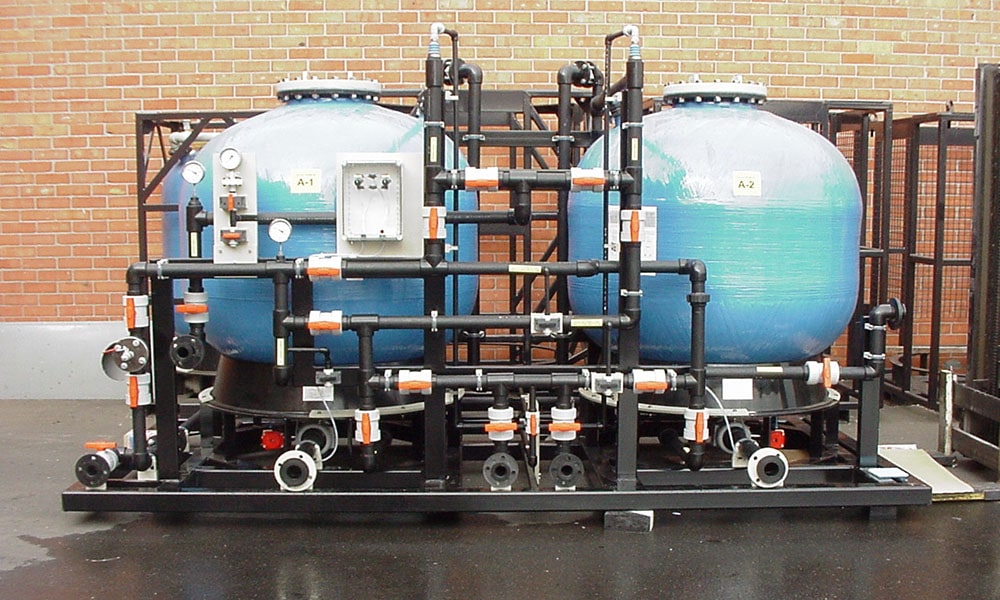
PURIFIED WATER AND WATER PURIFICATION SYSTEMS Standards
The main standards for pure water in pharmaceutical, clinical, bio-molecular and pharmaceutical activities include Pharmacopoeia, CLSI, CAP, ASTM, and ISO Pharmacopoeia standard is one of the most important standards used in cell production activities.
Two stabilized grades for pharmaceutical activities include Pure Water (PW) and Injection Water (WFI). In 2002, the European Pharmacopoeia EP introduced a new type of pure water called the very pure HPW. This is similar to the European WFI grade and is not used exclusively in distillation processes. The following are the characteristics of PW water, WFI, and HPW. PW and HPW water can be obtained by water supply systems.
Process and systems of purified water production
In the process of water purification, a pre-treatment water process is needed to achieve the following objectives.
- Prevent the formation of sediment and mass of eclipses by removing particles and organic and microbial impurities
- Maintaining the scale and operational size of the equipment levels by eliminating hardships and problems
- Removing materials used to control microbial substances such as chlorine
- The main techniques of the pretreatment process are usually filtration, softening the water (removing the initial hardness), treating with active carbon (organic matter removal) and adjusting the pH, which is done with water conditioning devices.
- Deep or membrane filtration is used to remove particles in the first stage. At this stage, the growth of microbes on the membrane of the filters should be controlled.
- The softening of water by ion exchange is one of the most common methods to prevent the dissolution of calcium-soluble salts with octant 2 and 3 capacities such as calcium carbonate and calcium sulfate at subsequent stages of purification. Passing through a bed of sodium-cation exchange resins leads to the replacement of most cations with sodium. Carbon dioxide removal can also be beneficial in an optional way by gas separation.
- The softeners can be used in the upstream and downstream areas for organic removal and disinfection. Using sodium-based resins, cation exchange to remove water hardness such as calcium and magnesium, which can cause problems and impairs the performance of downstream equipment, such as reverse osmosis, deionization and distillation unit.
- Water softeners can also be used to remove other cations with low enzymes, such as ammonium ions, which may be introduced into the water from chloramines used to disinfect it. If removal of ion amino is one of the objectives of the pretreatment process, water softening should be transferred after the removal of bacteria and organic matter (the end of the pretreatment process).
- The initial removal of organic impurities can be done by oxidizing with ozone, ion exchange, or membrane filtration. But the most important way to remove organic matter is to use activated carbon to absorb organic matter and remove chlorine and chloramine.
- The most important forms of carbon use in the pretreatment process are the carbon dioxide supply for germs and the growth of bacteria on its high surface.
Principal methods of water purification
A wide range of processes with different makeup can be used to produce pure water with a pharmaceutical grade. In the following, a few of the main processes are briefly introduced. In the following, a few of the main processes are briefly introduced.
-
Reverse Osmosis (RO)
In the reverse osmosis process, a pressure switch of 30 to 60 times to pass water and other molecular molecules with low molecular weight through a semipermeable membrane will be used. This membrane is resistant to ion passage and acts as a wall for colloids, bacteria, endotoxins, and other large organic molecules. This is a basic way to remove more than 90 percent of impurities. The features of this method are presented in Fig. 3 in combination with the method of electro deionization.
-
Electro deionization (EDI)
Deionization with the electrode does not require a chemical reduction of the resin than the conventional ion exchange methods and thus provides a stable purity. The basis of the process in EDI is the removal of ions through the passage of water from an ion exchange resin bed under the influence of the electric field DC. The resin bed is confined to an anionic or cationic resin, which allows the passage of anion or cation ions but does not permit simultaneous passage. There is a large variation in the design of EDI systems that use mixed or single resins. The following illustrates how the RO process completes with the EDI process.
-
Ion Exchange IE
Ion exchange is used more in the old processes. Two-bed systems are very effective in eliminating ionic mass contamination. Mixed-mode systems create the most ionic purity. When the power of the ion systems is reduced, they must be rehabilitated by the chemical recovery of acid-exchange cation exchanger systems and anion-exchange systems. For small-scale ion exchange systems, one-use substrates are used. UF ultrafiltration
-
UF ultrafiltration
During the ultrafiltration process, water passes through a fine filtration membrane (usually with a porosity of 2 to 50 nm) at a pressure of 2 to 10 bar. The filter prevents the passage of particle and large molecules, including bacteria and endotoxins.
-
Microfiltration
Microfiltration is usually used to preserve microbial residues in the downstream process, which is likely to be present. The porosity of the filters is between 0.1 and 0.45 microns, which is very effective. However, these filters do not prevent the passage of endotoxin and other similar molecules. If the concentration of bacteria on the filter plate increases, the probability of releasing endotoxin also increases.
-
UV light
Ultraviolet light at a wavelength of 240 to 300 nm leads to the destruction of DNA from microorganisms, which ultimately leads to the destruction of the organism. Exposure of purified water to a suitable dose of UV light can greatly affect bacterial effects and can be used as a final treatment step after other purification processes However, light UV has little effect on endotoxins.
-
Distillation
Distillation can be used to remove the impurities when the appropriate pretreatment process is performed on the water. Due to high energy consumption, the use of large-scale distillation is limited to the production of WFI. Because the distillation process is a requirement for the production of WFI based on the European Pharmacopoeia standard and the American standard. Distillation can result in more than 99.9% reduction in bacteria and endotoxins with high effects.
Evaporates in the distillation of water and produces a high vapor content of solid and non-volatile solids. Volatile substances and molecules with low molecular weight, such as endotoxin, enter the water droplets in the vapor phase. These drops are separated from the vapor phase before condensation. The proper pretreatment process in the distillation prevents eclipse and clogging of the surfaces as well as corrosion and prevents excessive bactericidal and endotoxin contamination.
Based on USP requirements, injectable water should be removed by distillation or by a purification method that is distilling or superior to it. This water should also be tested for TOC and cadavers, and its bacterial endotoxin level should be below 0 25 (ml) units of the endotoxin unit. The level of microbial contamination should not exceed 10 CFU per 100 mm.
-
Cleaning the sanitization system:
Microbial control is carried out in clean water systems through cleaning operations. The system is cleaned by thermal and chemical methods. In the Pharmacopoeia, there are some considerations about the temperature of the circus and its duration. Suitable chemical methods can be used in a wide range of equipment. These methods are usually performed using oxidizing agents such as hydrogen peroxide ozone and other similar materials. Description of cleaning with chemicals is also referred to in Pharmacopoeia.
-
Water distribution systems (Loops)
WFI / PW loops are used to generate and distribute this type of water at different points of the unit. A typical distribution loop, including a storage tank, two parallel and alternate pumps, to maintain loop pressure, a flow control system for maintaining a constant pressure at multiple points of use, other axial elements such as high-pressure valves, Check valve, diaphragm valves, ultraviolet lamps (UV) and heat exchangers
The most important difference between loop PW and WFI is the storage temperature. Looped PW temperature is maintained at room temperature and WFI loop temperature in the range of 90-80 degrees Celsius. That is, WFI loops require heat exchangers (maintaining WFI temperatures).
Another important difference between the two loops is the need to cool the points of use in the WFI loop. The most important problems with WFI and PW loops are the physical, chemical and microbiological properties of water. For this purpose, the design and installation must be completely clean and drainable, and the components used must have resistance to the cleaning and sterilization processes.
For this purpose, the design and installation must be completely clean and drainable, and the components used must have resistance to the cleaning and sterilization processes.
Storage conditions are adjusted to prevent bacterial growth. So the water spins at a temperature above 80 ° C or in hotter sterilization conditions. Water should not be stagnant in the system, which is why it is constantly circulating and there is no possibility of stopping water in a path. The design and construction of pipes are free from dead space and the principle of “six times the diameter” (the larger the length of the branches is six times the diameter of the main tube) is applied.
Water under non-self-contained conditions (cold storage) should not be stored for more than an hour in the grass, but it is not difficult to circulate during this time.
In a series of pipes, the discharge conditions are created by placing the shaft towards the discharge points.
There should be a possibility of steam injection into the system If the system has many users, it will be used to reduce the risk of possible contamination and also to better control the hydrodynamic conditions of several sub-loops at the point of use. These points should be sterilized before the water starts to run.
In addition to designing and manufacturing of PW generators, Mahyaz Engineering Company offers its customers the design, implementation, and documentation of loops for PW and WFI.