هر گونه عملیات شیمیایی نیاز به نوع خاصی از آلیاژ دارد که بتواند در مقابل خوردگی مقاومت کند و عاری از آلودگی یون های فلزی باشد. کاربردهای زیستی حتی ممکن هست نیازمندی های سخت گیرانه تری نیز داشته باشند، چرا که در این مورد درجه بالایی از تمیزی چه برای مواد استریل و چه غیر استریل مورد نیاز است. در مورد لوله کشی خطوط و پایپینگ خصوصا زمانی که محصول با سطح در تماس است، نیز همینطور است. فولاد ضد زنگ مشخصا شرایط لازم را در بردارد.
فولاد زنگ نزن نه تنها از آن جهت که طول عمر بالایی دارد، در دسترس است و قابلیت ساختش آسان است بلکه خاصیت ضد خوردگی و ضد آلایندگی دارد و می تواند در حالی که بسیار محکم و سخت است، به راحتی تا رسیدن به پایین ترین صافی سطح ممکن پرداخت گردد. فولاد ضد زنگ می تواند در مقابل عملیات حرارتی، شیمیایی و استریلیزاسیون مقاومت کند و در عین حال به راحتی جوش داده شود.
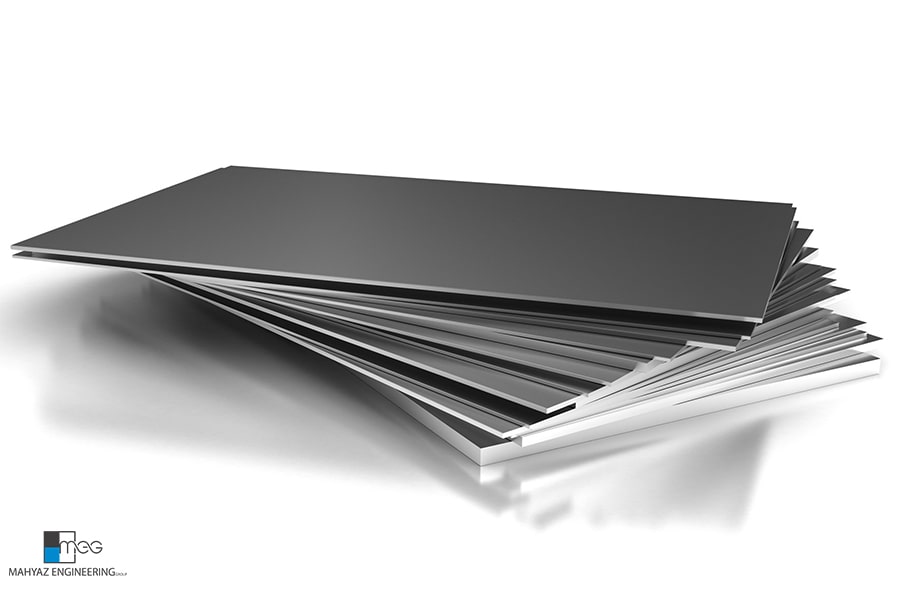
انواع فولاد ضد زنگ
حدود بیش از 70 نوع استاندارد فولاد ضد زنگ و آلیاژهای خاص آن وجود دارد، این فولاد ها (استیل ها) به شکل کار شده ( Wrought form ) و یا آلیاژ ریخته گری ( Cast alloy ) وجود دارند. همگی عموما پایه آهنی دارند همرا با 12 تا 30 درصد کرومیوم، 0 تا 22 درصد نیکل و مقادیر بسیار کمی از کربن، کلومبیوم، مس، مولیبدنیوم، سلنیوم، تانتالیوم و تیتانیوم. در ادامه به توصیف پرمصرف ترین فولادهای زنگ نزن در صنعت خواهیم پرداخت.
فولاد های زنگ نزن کار شده
مارتنسیتیک (Martensitic)
این دسته از استیل ها که با عملیات حرارتی سختی پذیر و دارای خاصیت مغناطیسی می شوند در مقابل اکسید شدن مقاوم هستند. نوع 410 مشخص ترین مثال از این نوع است. این آلیاژها دارای 12 تا 20 درصد کرومیوم همراه با مقدار کنترل شده ای از کربن و سایر افزودنی ها هستند. خاصیت خوردگی آنها پایین تر از فولادهای زنگ نزن آستنیتیک بوده و عموما در محیط هایی با خوردگی ملایم استفاده می شوند.
فریتیک (Ferritic)
این نوع از فولاد ضد زنگ ذاتا خاصیت مغناطیسی دارند (به دلیل وجود ساختار آهنی) اما با عملیات حرارتی سختی پذیر نمی شوند. دارای 15 تا 30 درصد عنصر کرومیوم هستند و میزان بسیار کمی (حدود 0.1 درصد) کربن دارند. میزان بالای کرومیوم در این استیل ها باعث بهبود مقاومت خوردگی شده است. مثال رایج این دسته نوع 430 است که در واحدهای نیتریک اسید تولید می شود.
آستنیتیک (Austenitic)
عمدتا در فرآیندهای زیستی استفاده می شوند، ذاتا غیر مغناطیس است، با عملیات حرارتی سختی پذیر نمی شوند، و بیشترین مقاومت خوردگی را در بین سه گروه دارند.
بیشتر انواع فولادهای آستنیتیک فولادهای آلیاژی هستند، فولادهایی که خاصیت آلیاژی کمتری دارند و در آنها منگنز با نیکل جایگزین شده است (سری 200) و گروه 18-8 که تیپ های 304 و 316 و انواع آن را در برمیگیرد.
انواع 304L و 316L مواد پرکاربرد صنایع دارویی و زیست فرآیندی است، در این نوع میزان کربن تا حدود 0.03 درصد نیز کاهش پیدا کرده است که موجب جلوگیری از ته نشینی کرومیوم کاربید می گردد. این استیل ها زنگ نمی زنند، به راحتی جوش می خورند و ماشین کاری می شوند و در زمانی که خلوص و کیفیت مواد اولیه به درستی لحاظ گردد به هیچوجه واکنش نمی دهند و خاصیت جذب کنندگی و یا افزایندگی نخواهند داشت.